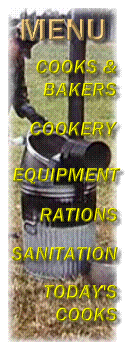
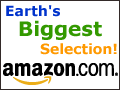
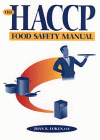
|
Field Dishwashing
Tips
Reprinted from Chapter 5 of Logistics
Support for the Naval Construction Force: Field Messing,
Seabee Logistics Training Guide Series, Module No. 7.
The following tips are based on the
experience of Seabee MSs. When followed, they will help
make a field mess operate in a sanitary manner.
Pallets -- Use pallets or similar
flooring material under the immersion heaters.
This provides a stable platform for the garbage
cans. It is very helpful in wet weather.
Thermometer -- Issue a pocket
thermometer to all MSs as well as the leading
food service attendant for each immersion heater
crew. Train them to check temperatures often as
needed to ensure proper temperatures are
maintained.
Keep the water trailers full --
Coordinate with Alpha Company to keep the 400
gallon water trailers full. A NMCB field mess
uses large quantities of water each day. It is
upsetting to arrive at work at 0300 to find the
water bulls empty.
Pre-fill cans -- Pre-fill the
garbage cans with 20 gallons of water at the end
of each meal or washing cycle. Cover each can
between meals. This way the immersion heaters are
ready to light. This is very important in the
morning before breakfast when you do not have a
lot of time to fill the cans and heat the water.
Drain cans -- Instruct the
master-at-arms to have immersion heater crews empty
all immersion heater cans at the end of every
meal. Do not attempt to conserve this water.
It is important to start each meals with fresh
wash and rinse water.
Instruction signs -- Post signs
next to each immersion heater with clear, concise
instructions on how to prepare that can for use.
An alternate method is to stencil the can
designation, water temperature, and amount of
hand dishwashing detergent directly on the can.
This helps food service attendants, who are often
assigned to the mess for a short period in the
field, do their job correctly.
Drying table -- Use one or more
tables as drying tables. If enough tents are
available, use a tent to shelter the pot and pan
storage area. Set up drying tables in a location
where smoke and soot from the immersion heater
stacks does not fall on the equipment. Be sure to
cover equipment at the end of the washing period.
Sheet plastic -- Take a roll of
heavy sheet-plastic to the field and use it to
cover equipment after washing. This is especially
helpful when equipment must be stored outside. It
minimizes the need to re-wash equipment that gets
dirty due to field conditions.

|